The Process of Creating a Stacked Glass Sculpture
- lindanamniece
- Aug 27, 2024
- 6 min read
Last month, we explored the integration of stacked glass sculptures into interior design, highlighting how unique materials and innovative techniques elevate space's design. However, the art of stacked glass sculpture itself is a meticulous and complex process, requiring both patience and precision to create pieces that are not only visually stunning but also enduring and sustainable.
Over the past 13 years, Ernest has spent refining his artistic approach not only to strive for the highest quality, while continually developing more environmentally conscious practices. Below, we outline the eight phases involved in creating a stacked glass sculpture—a journey that blends traditional craftsmanship with cutting-edge technology.
1. It All Starts With a Sketch
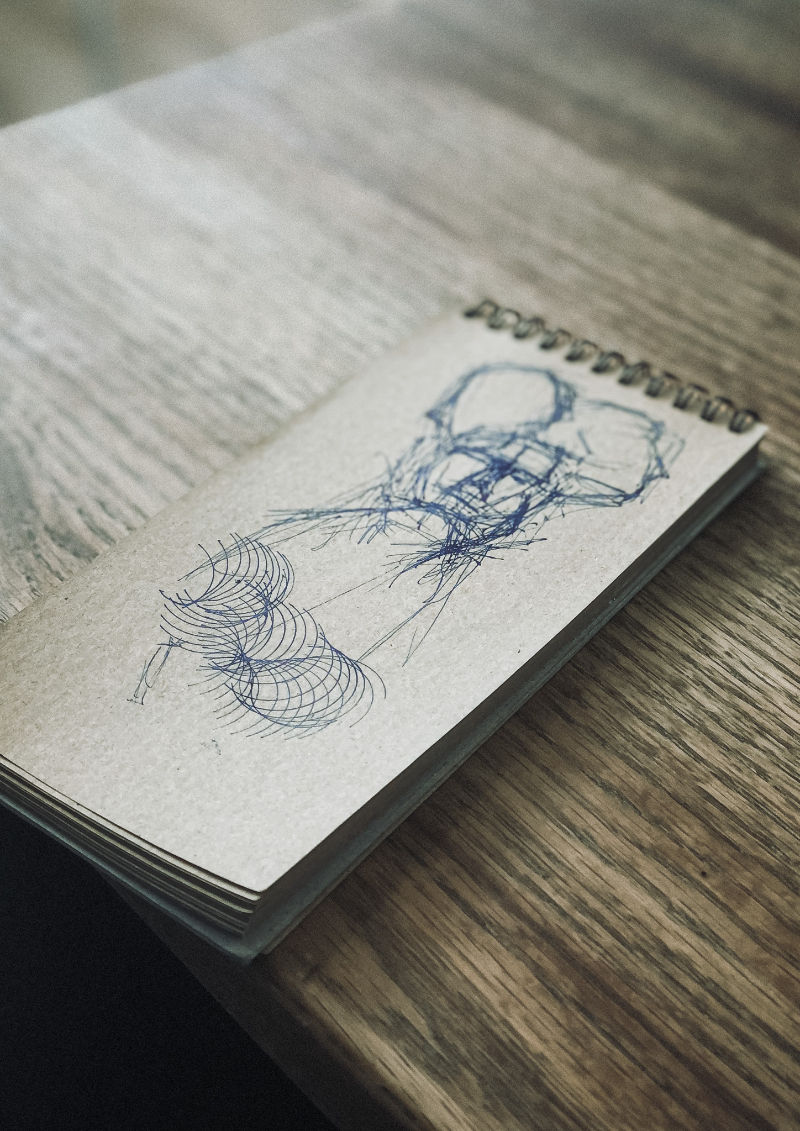
The initial sketches are where ideas take form, with limitless possibilities waiting to be explored. However, these creative visions must be grounded in practicality. As the initial concepts are developed, considerations such as structural integrity, spatial dynamics, and the intended environment play crucial roles. This phase is where imagination meets reality, laying the groundwork for what will come next: planning (for commissions) and 3D modelling.
2. Planning the Artwork: For Commissions and Exhibitions
In the planning phase, the conceptual design is meticulously refined to ensure it aligns with both the client’s needs and the functional requirements of the space. Factors such as floor load capacity, safety, size, and budget constraints are carefully evaluated. This stage is critical, as it determines how the sculpture will interact with its environment and ensures that it complements the existing architecture. When the plan is finalized and all parties are satisfied with the artistic vision, we transition to the creation of a 3D model—a crucial step in bringing the design closer to reality.
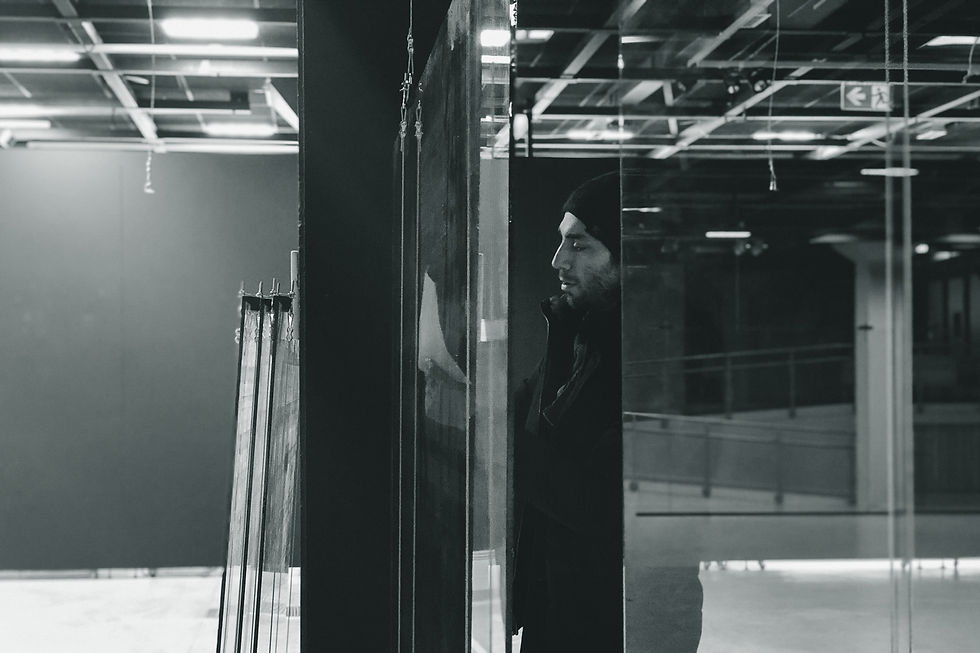
3. Modelling the Form of the Stacked Glass Sculpture in a 3D Software.
Sketching is beautiful, but it never reflects the reality. The proportions of the sheet glass and the technical possibilities of cutting and shaping it come into play when creating the final form of the sculpture. This requires developing a 3D model, a process that can take anywhere from 1 to 2 months. If the sculpture is based on an existing design, adjustments to the model typically take 1-2 weeks.
With advancements in technology, Ernest can fully rely on 3D modelling software to develop precise digital models of the sculptures. Previously, foamboard prototypes were used for 1:1 models, but these were limited in their ability to accurately reflect how light would interact with the glass. By transitioning to digital models, we enhance both the precision of the design and reduce material waste, aligning our process with sustainable practices.
Once the 3D model is approved, we move to the CNC phase, where the digital model begins to take physical form.

4. Tracing onto glass with a CNC machine: Integrating Craftsmanship with Technology
The CNC (Computer Numerical Control) phase involves creating 3D technical drawings for each glass layer, which are then input into the CNC machine. This machine precisely traces the design onto large glass sheets, ensuring that each layer is perfectly aligned and optimally arranged for cutting.
CNC technology not only improves the accuracy of our work but also maximizes material efficiency. By optimizing the spacing between elements, the CNC machine allows us to use glass resources more effectively and reduce the time previously spent on developing polystyrene prototypes.
CNC drawing preserves the handmade artisan quality of traditional methods while embracing the efficiency and precision of modern technology. Watch this video about CNC on EV's Youtube channel.
5. Glass Cutting: The Art of Precision

Cutting the glass layers is where craftsmanship truly shines. This phase requires careful planning and strategy, as each glass sheet is hand-cut using a glass cutter, hammer, and breaker-grazier pliers.
The glass cutter is used for scoring—a technique where a line is traced onto the glass sheet with a sharp blade. Then, with a light tap from the hammer, the glass is broken along the scoreline. Although it may appear straightforward, achieving the desired result for more complex pieces demands immense patience and skill honed over many years.
The process of cutting the glass varies depending on the complexity of the sculpture, involving diverse cutting strategies and edgework. For intricate pieces, only 2-4 layers may be cut per day. Once the cutting is complete, the glass undergoes grinding, glueing, and additional edgework to prepare it for the next phase.
6. Grinding and Polishing - Integral to Stacked Glass Sculpture creation
Given the specific forms and textures of our glass sculptures, there is no automated machinery capable of achieving the results Ernest Vitin's art studio requires. Instead, his team relies on their handmade tools and the expertise of their own.
For an average-sized glass sheet with a perimeter of 150 cm, up tp 30 minutes are spent for grinding.
Grinding and polishing are performed with an average of 4 different tools - various-size handmade belt sanders, an angle grinder and a drill. Sanding belts and grinding discs with grit sizes from #200 up to #1500 are used to preserve the rough texture, ensuring its characteristic appearance is maintained while simultaneously eliminating hazardous sharp edges. The higher the grid number, the finer the result. Metal grinding discs, cylinders, and balls are often used to smooth and refine the borders, creating a safer and more aesthetically pleasing finish and fine-tuning the detailed features of the sculpture.
To achieve full transparency, a special polishing paste is applied with felt wheels. This step ensures the glass reaches the desired level of clarity and brilliance. After stacking the layers, we conduct a final round of grinding to perfect the sculpture’s finish.

7. Gluing – Paramount Process in Ensuring the Quality of Stacked Glass Sculpture
The bonding of the glass stack is the most complex and critical stage in the creation of stacked sculptures. During the bonding process, the craftsman must work with intense concentration, as any distraction could lead to a mistake that would mean starting the entire process from the beginning.
For each layer, a considerable amount of adhesive is applied to each glass sheet to ensure that the entire surface is fully covered after the next sheet is placed on top. Every layer must be measured with a digital level to ensure an even application of the adhesive. Glueing in this manner is essential to ensure the highest quality and endurance of the artwork.
Lastly, to achieve the necessary precision in the glueing process, we create custom stands for each sculpture. They are uniquely tailored and cannot be reused. Unfortunately, after the bonding, these stands have to be broken to release the bonded glass parts.
8. Cleaning the Sculpture from Excess Glue
After the adhesive has been bonded with UV light, any excess glue must be meticulously removed—a process that is both time-consuming and labour-intensive. Cleaning a 1.5-meter tall sculpture can require up to 100 hours of careful handwork. For each square meter, depending on the complexity of the sculpture's shape, the cleaning process alone can take approximately 30 hours. Once this painstaking stage is complete, only the final touches remain to bring the sculpture to its polished, finished form. Watch this video on the process of cleaning the glue on my Youtube channel.
9. Final Touches: Bringing the Artistic Vision to Life
The final phase involves adding the finishing touches, which includes a final round of grinding, polishing, and cleaning to ensure the sculpture meets the highest standards of quality and aesthetics. The physical creation of the glass sculpture, on average, takes 2-3 months. This applies to sculptures like Fallacia, Sophia, which are up to 180cm in height, weighing 150kg. Larger ones would take longer. For example, Budding Flowers would take about 5 months. For truly large projects, like In Nature, we involve additional help and adjust all workshop activities to the large project, completing the entire composition within 9 months.
Conclusion
Creating a stacked glass sculpture is a journey that requires a blend of artistic vision, technical precision, and meticulous craftsmanship. From the initial sketch to the final touches, each phase of the process is crucial in bringing the sculpture to life. This meticulous approach ensures that every piece not only meets the highest standards of quality but also contributes to a sustainable and enduring work of art.
As we continue to explore new technologies and refine traditional techniques, the potential for innovation in glass sculpture expands. For architects, designers, and project managers, understanding the complexities and craftsmanship involved in creating these sculptures offers valuable insights into how they can be integrated into modern architectural spaces. The result is not just a visually stunning piece of art but a lasting statement that enhances and elevates the environments it inhabits.
Comments